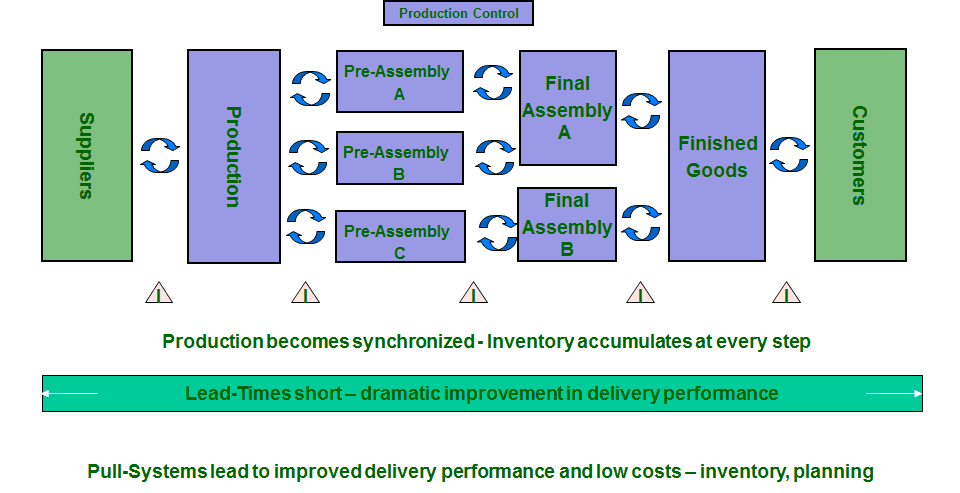
The Kanban principle (Kanban definition) was originally developed in 1947 by Taiichi Ohno in Toyota Motor Corporation. It is a system for control of material flow and production according to the “pull principle” (also pick-up principle). In this case, so-called self-steering control loops are employed to ensure the material supply.
“Kan Ban” itself actually means nothing more than “card”, “document”, “sign”.
Traditional Kanban systems usually use Kanban cards as the information carrier in a loop to control the production process visually. Here, a kanban corresponds for a production order for internal or external suppliers.
All details of the order are described on the card such as the part number and description, the number of parts in the container, the consumer (sink) and the supplier (source). Other relevant information can be included also.
A Kanban is a result of the smallest unit for each component or item group. Depending on demand, lead time and the desired safety stock parameter it can be calculated using a simple formula. As load carriers e.g. mesh boxes, pallets, SLCs, boxes etc. can be used.
When the last item is taken from the container (at some companies also the first item), the Kanban signal in form of a Kanban card or a container Kanban will be sent from the consuming station (sink) to the generating station (source). After refilling the defined unit, the full Kanban container is being returned to the place of consumption. The parts are then being provided in the so-called Kanban supermarket. This creates a cycle or Kanban loop.
The visualization of the production order is created by the empty container at the appropriate area or by a Kanban board, in which the cards or orders are sorted in. If there is “no” Kanban signal, meaning no production order, “nothing” will be produced.
Without any doubt, nowadays the much more modern methode is to use an “electronic Kanban Board”.
Advantages of the e-Kanban System:
- Minimal planning and control costs
- Low stocks of each production stage
- Controlled inventory
- Increase of the materials availability
- Improvement of delivery performance
- Shorter delivery times to the customer
- Reduction of cycle time
- Increase of quality
LEAN / KANBAN
Click on the desired topic to learn more.