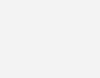
Flextronics is one of the biggest EMS suppliers of the world and is present with locations in 30 countries on five continents worldwide.
An electronic Kanban system supports Flextronics to fulfill customer wishes even better and to supply its customers‚ ‘on demand’.
„In 2002 we searched the market for a software system which would support us fast on our way to the world class production based on the Pull principle. We wanted a system, from which all employees of the company, from the manager to the material manager, will profit from“, according to Stefan Osswald, who is responsible for continuous improvement processesin Flextronics worldwide.
Some of the challenges were
- in the quick implementation through simple IT structure
- in the low training expenditure
- in the availability into all languages
- in the simple uses at production level
- in the reduction of the planning expenditure the the minimum
Due to the implementation of a Kanban system the enterprise wished: a reduction of the inventory and as a result of it the storage place demand needed and related costs, increase of the inventory turnover and the material availability, reduction of the delivery times and the reduction of the planning expenditures.
The choice of the supporting software fell, finally, on the Integrated Kanban system (IKS) of the manufactus Ltd in Starnberg.
IKS allows the setup, dimensioning and optimisation of Kanban loops in the entire company. The multilingual features and user friendly interface are significant factors to get acceptance of the system by employees at the production.
As the result the capture of the Kanban movements through bar-code scanner ver high transparency of the production could be reached, input errors have been avoided. The flow of the Kanban signals electronically reduces the transfer times to the minimum and overcomes long distances from country to country. The passing on of the Kanban signals on electronic way reduces the transfer times to a minimum and, besides, bridges also long ways from country to country.
Electronic Kanban boards priorities the orders for some areas and machines and point to the employees which parts must be produced as a next ones. As a result of it a big number of articles or Kanban cards can be easily handled.
Because Flextronics must react as quickly as possible to changes in product and the amount, it is absolutely necessary for the production process to adapt the amount of the Kanbans immediately in order to keep the inventory at low level.
The so-called IKS Demand manager supports the production responsible employees by the automatic calculation and adjustment of the Kanbans.
„The achieved flexibility is the key to the inventory control, and additionally the system significantly contributes to the fact that increase of the inventory is avoided“, according to Osswald.
In order to check whether the available machine capacity is sufficient, the IKS capacity module is employed, which compares available to the required capacity and gives a quick overview over possible bottlenecks. If these occur, Kanbans and production capacities can be shifted fast and in an easy way from one machine to another. Due to several diagnosis and audit processes the system allows a stable optimisation of the inventory, material availability and as a result of it also the customer service.
With IKS all Kanban processes are supported in the production and additionally a lot of other information is delivered for all employees. Thus, the smooth production is ensured – a success for the customer as well as for the enterprise.
After a pilot project in 2003 at Guadalajara, Mexico, Flextronics began the worldwide implementation. Meanwhile the IKS is installed in 15 plants of the enterprise worldwide, where support for many languages has a great impact in acceptance of the software, especially in China.
„Flextronics has achieved significant savings due to implementation of the IKS . The inventory and as a result of it the needed storage requirements have decreased by around half, the material availability equals at the moment more than 99% – savings in a company of our size go into the millions “, according to Osswalds conclusion.
More case studies
Click on the desired case study to learn more.