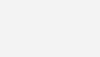
The IKS KANBAN ANALYZER is an add-on module of the IKS base system and allows a directed and continuous analysis and optimization of the Kanban system.
In a classic manual Kanban system, the parameters of Kanban dimensioning (demand, lead time, safety factor, container content) are set at the very beginning. A review whether these factors are still correct, and as a result whether the amount of Kanbans is still correct, in most cases this is related to a lot of expenditures and time effort.
If the Kanban dimensioning is wrong, this has some serious implications:
- Kanban amount of an items is too low: risk of missing parts (constantly)
- Kanban amount of items is too high: too high stocks and as a result a potential to optimize
The IKS Kanban Analyzer provides a variety of predefined reports and ratios to monitor the Kanban system continuously with less time effort and as a result to optimize it quickly.
The evaluation includes:
- Current and historical inventories and their trends
- All measured times such as lead times, production times, waiting times, etc. (by scanning the Kanban)
- Stock ranges
- Material envelopes
- Delivery reliability
- Control mechanism for production and external suppliers
- Current Kanban Master Data
- and much more
Your advantages are:
- Material availability is ensured (100%)
- Simultaneous optimization of inventory
- Monitoring of delivery times and delivery reliability of your external suppliers
- Optimization of Kanban container sizes
- Simple and clear control of the Kanban system (internal and external processes)
- Documented analysis (with extensive charts and reports)
IKS Kanban Modules
Click on the desired topic to learn more.